Extrusion Process
At Teufelberger we see ourselves not only as manufacturer of high performance straps, but as a partner for all strapping users. Partnership means for us sharing knowledge and exchanging experiences. That is what you can find here, our brainBox, with insights on technical information, product tests and descriptions of our world of strap making.
The overview is designed to help non-technicians and industry professionals alike to understand frequently used terms and concepts of PP and PET strapping.
Extrusion Process
A PP or PET strap has to go through several stages in the extrusion process before it is finally ready for use as packaging material.
Here is a simple explanation of the steps required.
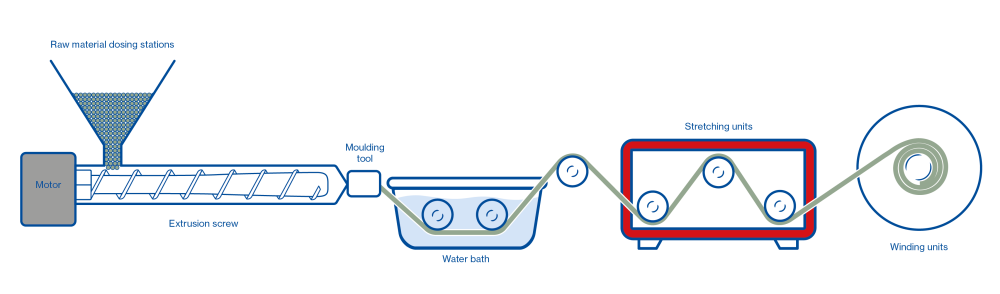
- Raw material dosing stations
Dosing stations are used to create the desired material mix of granules or PET flakes.
The material mix depends on the desired properties of the strap. - Extrusion
The machine heats and melts the plastic granulate or PET flakes using an extrusion screw. The combination of heat and pressure transforms plastic into a molten mass. The melted plastic is then forced through a specially designed extrusion or moulding die.
- Cooling through a water bath
After exiting the die, the molten plastic enters a cooling section. In this section there is a water bath in which the molten plastic cools and solidifies quickly.
- Stretching units
After cooling, the plastic strap may pass through additional stretching units as rollers or ovens to ensure it has the correct width, thickness, elongation and surface finish. It may also be embossed or waxed, if required.
- Winding units
The continuous strap is then wound on paper cores to finally get the coils with the desired length.
- Quality Control
Throughout the extrusion process, quality control measures are implemented to monitor the strap's properties. This may include checking for thickness, width, and breaking strength. Any inconsistencies are usually identified and addressed during this phase.
Breaking Strength
Breaking Strength or break strength is the force the strap can withstand, i.e. indicating the pressure before it breaks. On the market it is often referred to as break load.
The breaking strength of a plain, unused strap is shown on the datasheet with minimum and average values. The unit of the breaking strength is kilogram / pounds (kg / lbs) for plastic strapping. Coming from the steel strap industry, its tensile strength is given in break load / cross section (N/mm²).
As the breaking strength can be measured it is a crucial parameter for strapping.
Strap Joint
A strap joint, also known as a weld joint, is the connection between the two ends of a plastic strap. The weld joint can be created through either vibration or heat tongue sealing, depending on the technique used by the strapping machine.
Did you know that the strength of the strapping is only as strong as the weld joint? This means a weak or poorly executed weld joint can significantly reduce the overall strength of your strap, making it the most likely point of failure.
Strap Joint Strength / Weld Joint Strength
The weld joint strength indicates the quality of the connection between the two plastic strap ends until the weld breaks. It is measured in Newtons (N) and is always lower than the indicated breaking strength of the plain, unused strap, as provided on the datasheet.
The value of the weld joint strength is influenced by the adjustment and settings of the machinery in combination with the strap material used.
Strap Joint Efficiency / Weld Joint Efficiency
The weld joint efficiency, sometimes referred to as weld efficiency, strength efficiency, or breaking load efficiency, is expressed as a percentage. This value represents the ratio between the weld joint strength and the breaking strength of the unused strap.
For comparison:
- High-quality PET straps can achieve a weld joint efficiency of 70-80%. In practice, this value can vary widely and typically ranges from 30-80%.
- PP straps have a much lower strap joint efficiency, averaging around 40%.
Stay curious and keep coming back – we regularly update our content to ensure you have the latest information. If you have any open questions regarding strapping please feel free to contact us at strapping@teufelberger.com.
We are here to ensure you have all the information you need to make informed decisions and better understand our products and services.