...my rope gets too hot?
One of the main questions in the rope world is “Is my rope still good to work with?” Manufacturers specify a theoretical service life in their instructions for use. This is mainly based on very rare use. The actual service life, especially when the rope is heavily used, depends on a lot of factors that are beyond the control of manufacturers. In this series, TEUFELBERGER presents the results of a study made on “Deliberate damage of ropes”. In this article, we want answer some frequent questions on the influence of temperatures and share the results about the topic of “Heat resistance”.
Two different scenarios can occur when ropes are exposed to heat. First, ropes can get in direct contact with heat through hot surfaces. For example metal surfaced that are heated by the sun or any other heat source. Second, ropes can also be exposed to heat from the environment, when working in hot surroundings. One extreme example is an expedition into Masaya Volcano in Nicaragua, done some years ago.
No matter what scenario occurs, exposure to heat brings ropes very quickly to their limits. In the table below, you can see an overview of the heat resistance of different materials. In our tests, we conducted two main series to test the influence of heat on ropes. First, different kind of ropes were exposed to contact heat and secondly to surrounding heat.
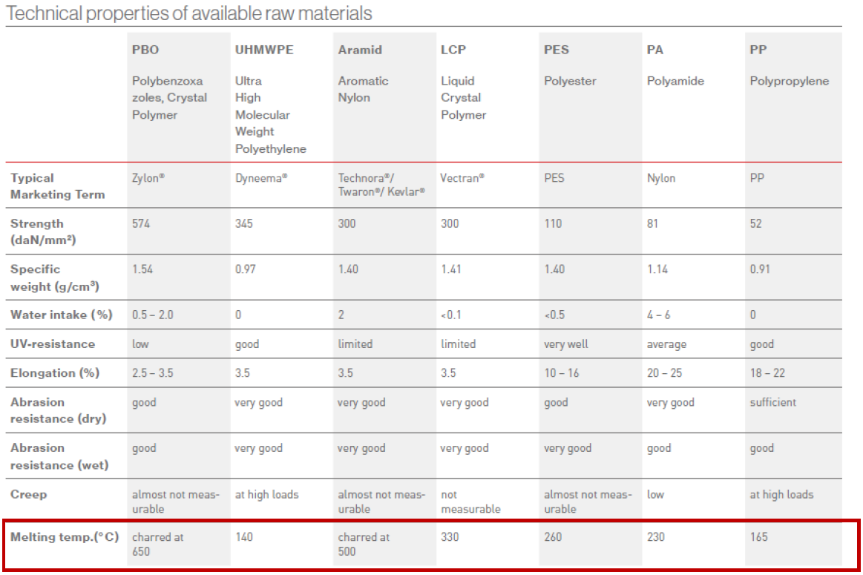
1. Contact heat
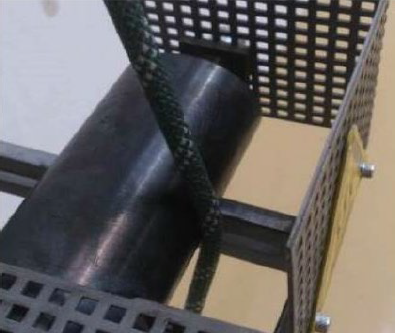
In all test series for contact heat, the rope was placed on a heated metal surface with a 3-bar pressure. Below you can see the test layout.
Pic.1 (le.): Test layout “Contact heat”
a. Polyamide ropes – Different times and temperatures
For the first test, the EN1891A Rope Patron 11mm was placed on the heated metal surface with 210°C for different times. After the exposure to heat, the rope was let to cool down and then tested for its residual strength. Visual damage was seen after a short period of time.
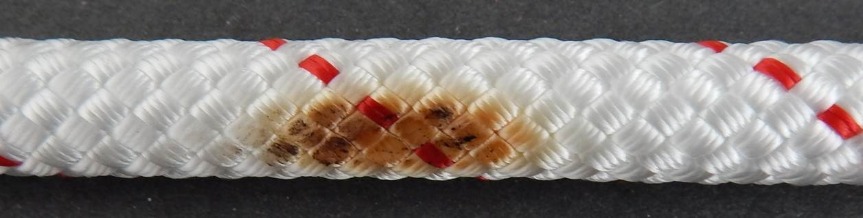
Pic.2: Patron 11mm at 210°C for 5 min

Pic.3: Patron 11mm at 210°C for 20 min
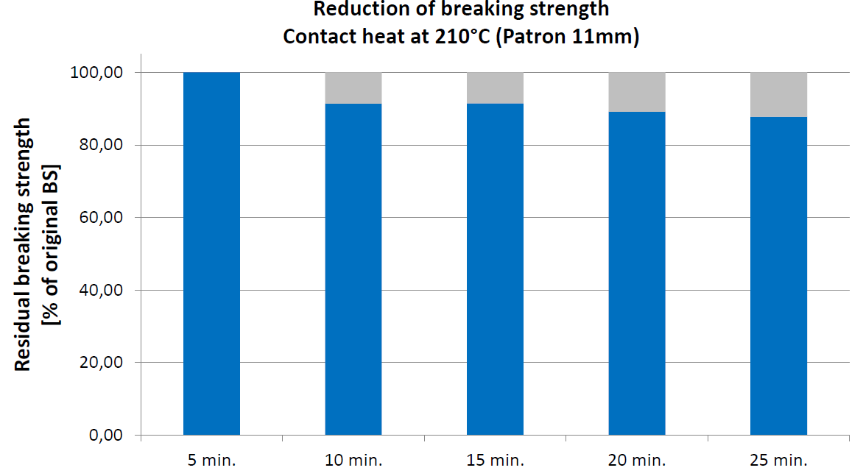
For further tests, the temperature was increased, the visual damage after one minute of exposure (Patron PLUS 11mm) is shown below. When the melting point of Polyamide is exceeded, the rope melts very quickly. Residual breaking strength of this samples was not tested.
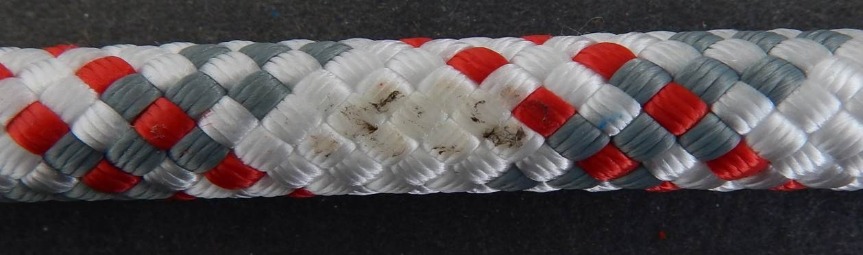
Pic.4: Patron Plus 11mm at 230°C for 1 min
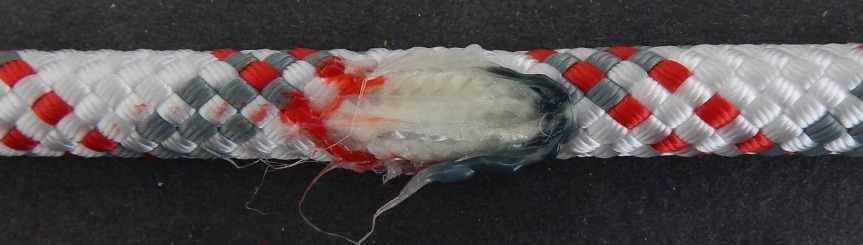
Pic.5: Patron Plus 11mm at 250°C for 1 min
b. Different ropes - 210°C temperature
For this test, ropes made from different materials were placed on the heated metal surface with 210°C for 10 minutes. After the exposure to heat, the samples were let to cool down and then tested for their residual breaking strength.
The following ropes have been tested:
- Patron 11mm (Polyamide core / Polyamide cover)
- Platinum Protect PES/PA 10,5mm (Polyamide core / Polyester cover)
- Platinum Protect PA 10,5mm (Polyamide core / Polyamide cover)
- Sirius 10mm (Polyester core / Polyester cover)
- Ocean Polyester 8mm (Polyester core / Polyester-Aramid cover)
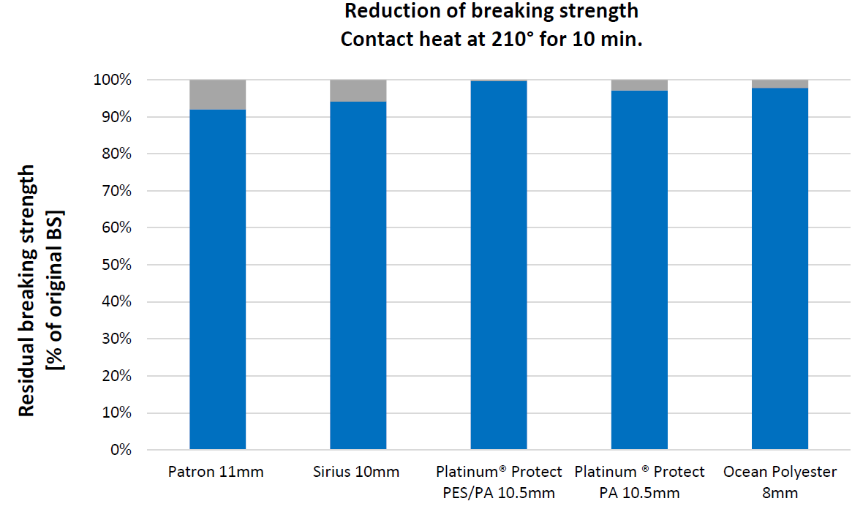
c. Advantage Aramid ropes
In order to demonstrate the increased temperature resistance of aramid, the ropes listed below were tested at a temperature of 280°C, which is above the melting point of Polyamide and Polyester. The goal was to confirm the benefits of aramid. The Polyamide rope broke after 30 seconds. of exposure, the Polyester rope after 3 min. Both ropes featuring Aramid in the core and/or the cover resisted the exposure time of 3 minutes. The loss in breaking force was still below 20 %.
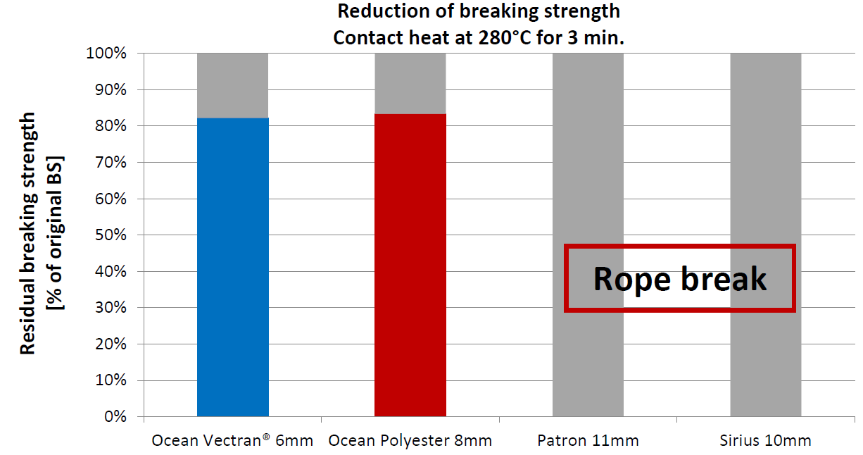
In addition to the test at 280°C, the rope samples were also placed on a heated metal surface with a temperature of 300°C. Then the time was measured until the ropes broke. The results show that there was s a significant difference in heat resistance between Aramid and non-Aramid ropes.
Rope | Time until break |
---|---|
Patron 11 mm | 1:05 min |
Platinum® Protect PES/PA 10.5 mm | 0:59 min |
Platinum® Protect PA 10.5 mm | 0:51 min |
Aramid Escape Rope 7.5mm | 15 min |
Vulcanus 10.5mm | 15 min |

Pic.6: Patron 11mm – Rope break at 300°C
2. Environmental heat
For the tests of resistance again environmental heat, the following rope samples were placed in front of a spotlight. The distance to the source of heat was 15 cm, the samples were exposed for 10 minutes. The average temperature on the rope’s surface was around 80°C. Only Polyamide ropes showed light discoloration, on all other ropes, no changes were visible.

Pic.7: Patron 11mm – 15 cm distance, 10 min
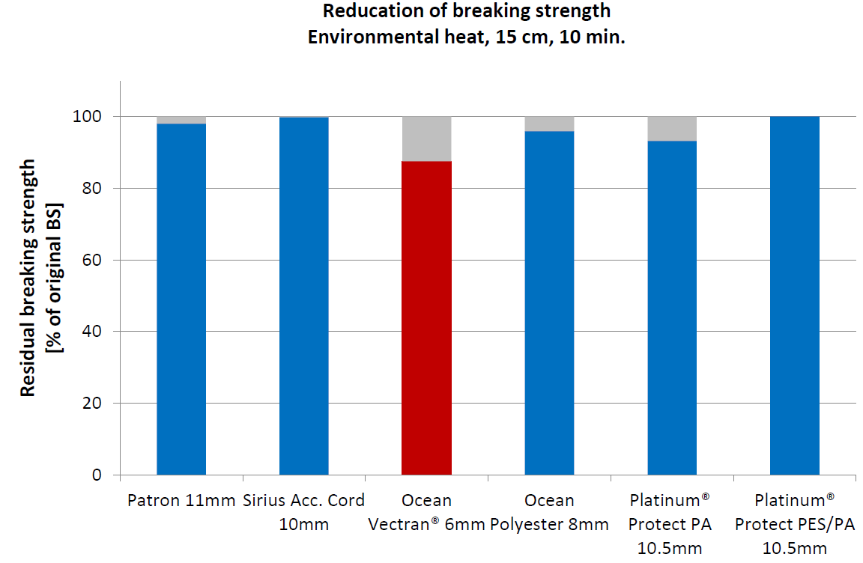
ATTENTION: Ocean Vectran did not break at the affected area but at the blocks where the rope was wrapped around for testing. A break in the affected area was not achieved .This implies that no reduction of breaking strength occurred due to environmental heat.
Conclusion& Recommendation
- In general, contact of the ropes with heat sources should be avoided.
- The heat resistance of a rope is dependent on its material and construction.
- For applications where higher temperatures may occur, it is strongly recommended to use ropes made of temperature-resistant materials such as Aramid.
- If a rope has obviously been damaged by heat (glazing of the surface, brown burn marks, etc.), the rope needs to be replaced.
- Coatings can add additional heat resistance to ropes.
- If there exists only the slightest doubt regarding the safety, the rope must be replaced!